MD321 / MD322 - Distortion measurement and wheel positioning
The MD321/MD322 machine is used for 100% process control measurement of alloy wheels before entering the CNC machining cell.
The machine is automatically loaded from an inbound conveyor. The cell robot picks up the wheel from the MD321/MD322 machine and then continues to load the wheel for subsequent operations. To shorten the installation and commissioning time, the machine is delivered completely cabled and tested. The measurement of the front face of the wheels is done with a laser scanner, mounted on a moveable X/Y-slide arrangement. The MD321/MD322 measures mainly the deviation of the front side clamping flange and the hub area. With the integrated wheel type recognition and individual type tolerance values, the machine can either be used in batch operation or at fully mixed production lines without any limitations. With the MD321/MD322 at the entrance at a CNC machining cell, only wheels within tolerance will be produced, and this will increase the overall output of the cell. The optional measurement of the clamping flange flatness and subsequent positioning on the chuck for clamping with the least wheel distortion at OP1 improves the overall wheel quality and significantly reduces unbalance of even the most difficult wheels. When using the NUMTEC barcode system, all measurements can be automatically linked for statistical reasons to a mold and a casting machine, which also monitors the overall performance of the casting area. The two machine versions MD321 and MD322 are basically supplying the same function to the process but supporting different cell layouts. If enough space in the cell is available, the MD322 will be installed such that the robot directly takes the wheel out of the machine gripper. If the space situation is more difficult, the MD321 can be installed outside of the cell and only the small gripper unit moves into the cell robot area for the wheel supply.
Your advantages:
- Distortion measurement: Automatic distortion measurement for individual correction of wheel deviation to increase product quality to improve the overall productivity rate of existing equipment.
- Mixed production: The machine can work in batch operation or in fully flexible production lines with mixed wheel types.
- NUMTEC barcode system / camera system: Wheel type recognition with NUMTEC barcode or optionally with design recognition camera system.
- Statistical data and trend analysis: All measured wheel data is stored in a database system. This system can be used to generate trend analysis of your production, i.e. for casting and heat treatment lines.
- Significant cost savings through quality improvement: With the laser flatness measurement of the outboard clamping flange and the calculation of the individual best chucking orientation at the CNC lathe, massive improvements in the overall wheel quality can be achieved.
- This will directly result in less rework percentage and NOK wheels.
Contact person
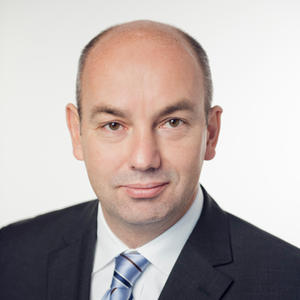