PF - Powder Feeder
The Mould Powder Feeder is designed for the automatic distribution of casting powder into the mould. This ensures a constant uniform mould powder distribution during the casting process.
The Mould Powder Feeder is applicable for all types of powder and granules. The Mould powder feeder is basically equipped with two feeding tubes and one powder container, installed on the carriage. The complete equipment is manufactured using standardised modules, which result in high reliability and low maintenance of equipment, and specially selected electrical and mechanical parts that are designed, well tested and proven to function in heavy industries.
The casting powder has to be filled manually into the powder container. To avoid clogging and to keep the powder dry, the powder container is equipped with a heating and a stirrer. The heating is mounted on the outer surface of the powder container. Inside the powder container the stirrer is mounted in order to get sure, that the powder slides into the feeding housings. In the feeding housing the powder will be transported by means of the feeding spirals through the outlet tubes over the mould.
The powder feeder will be moved manually to the working position in the way, that the ends of the feeding tubes with the outlets are located above the mould. The carriage is supported by two linear wheels and one flexible wheel. For adjustment of powder feeding height, these wheels can be fixed at different heights onto the carriage.
The stirrer inside the powder container further serves for the powder transport to the feeding housings. From the feeding housings the powder will be transported by means of the feeding spirals through the feeding tubes to the outlet tubes over the mould.
The powder output will be determined by the number of revolutions of the feeding spiral. The feeding spirals are driven by frequency converter controlled motors.
During casting process the powder feeding rate will be controlled according to the casting speed which is sent by the plant control system (Level 1). A capacitance proximity switch indicates the time for refilling the powder container. After casting or before a standstill the manual slides at the outlets of the powder container have to be closed and the feeding housing has to be emptied.
Your advantages:
- Wide application field: Usable for all types of powders and granules
- Low production costs: Low overall costs due to reduced and optimized consumptions of mould powder and saving manpower.
- Easy integration: Easy to integrate in existing casting floor
- Quality improvement: Constant mould powder distribution over the mould surface leads to an improved steel quality.
Contact person
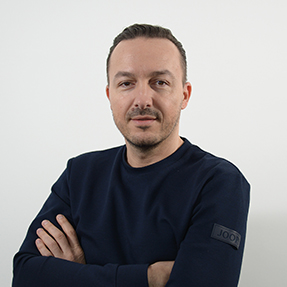
Markus Sternbauer
Head of Business Unit Steel
markus.sternbauer@alpinemetaltech.comRequire information