ABV300 - Inline sprue drilling machine
The ABV300 was developed for drilling out the sprues of aluminum wheels after the casting process. The powerful inline sprue drilling machine is unique on the market and sets new standards in terms of cost-efficiency and flexibility.
Usually, sprues are removed by punching, which can cause distortion and cracks in the aluminum. This risk is effectively prevented by drilling. In addition, drilling out the sprues allows considerably more possibilities in terms of the design and size of the sprue cross-sections. The robust spindle installed in the ABV300 can handle diameters of up to 100 mm, making it ideal for the big wheels and thicker material thicknesses in the hub area.
With the automatic tool changer and the integrated wheel detection system, each wheel is machined with the appropriate bore diameter. Bringing the bore diameter closer to the finished hub diameter achieves cycle time savings in the subsequent turning operations.
Optional features such as minimum quantity lubrication, chip conveyor or exhaust device allow individual adaptation to the different conditions of the production plants.
Your advantages:
- Inline machine
The ABV300 is installed directly in the conveyor line. The complete loading and unloading of the drilling unit is integrated in the machine. No external manipulator (e.g. robot) is required.
- Low material stress
Compared to punching, drilling causes far less material stress in the hub area. Even with large material thicknesses, there is no risk of distortion or cracking in the aluminum.
- Flexible production with tool changer
With the built-in wheel detection system and the fully automatic tool changer with integrated 12-tool magazine, each wheel can be machined with its optimum drilling diameter.
- Maximum throughput
Maximum production rates are achieved through consistent development for this application. With just one ABV300, approx. 4500 wheels per day with different hole diameters can be drilled.
- Cycle time savings in turning operations
The drilling diameter can be better approximated to the finished hub diameter. This saves valuable cycle time in the turning operations for wheel machining.
Contact person
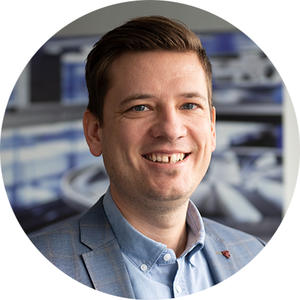